数控深孔钻切削过程要注意什么问题呢?
数控深孔钻在应用数量上在不断的增加,说起来现在市场的发展,跟扩展是比较往年要快很多,而且大部分的模具钢材行业需要应用到数控深孔钻,也很正产,因为质量的要求高,客户对质量要求高,自然这些数控深孔钻应用到的行业,质量也要做到位,对厂家的信誉,经济都会有影响。
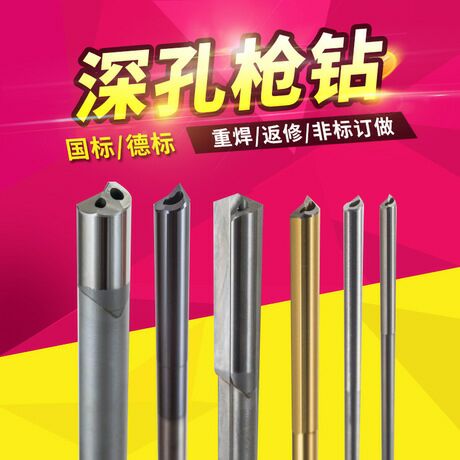
数控在数控深孔钻切削过程中,切肩在剪切平面上发生较大的塑性变形。同时,前刀面上的压力对切屑发生一个弯矩,迫使切屑弯曲。高速切削时,数控深孔钻前刀面的压力足够大。前刀面与切屑底面发生粘结,又因为切削过程是接二连三的,切屑底面的金属既伸长又不断的滑移,好像后浪推前浪,不和受压缩,促使切尼弯曲。切屑沿断屑台圆弧面弯曲,数控深孔钻其自在端可能与孔蹙、钻头或工件待加工外表相碰时,使切屑承受一个弯矩或扭矩而折断。 排屑速度快,适于高速切削。在排屑槽全长范围内,钻头直径是一个倒锥,钻削时与孔壁的磨擦小,钻孔质量较高。常见的钻柄直径有3.00mm和3.175mm.
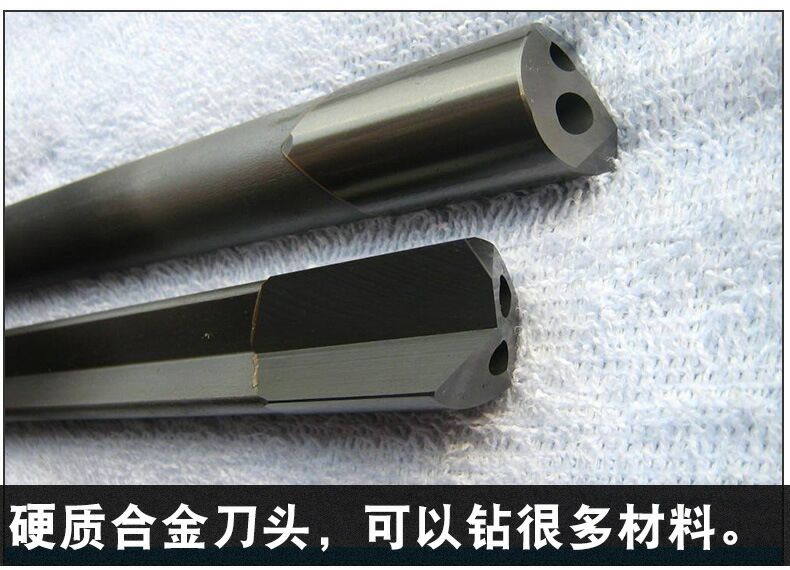
但韧性差,十分脆,为了改善硬质合金的性能,有的采用在碳化基体上化学汽相堆积一层5~7微米的特硬碳化钛(TIC)或氮化钛(TIN),使其具有更高的硬度。模具深孔钻加工时孔径增大发生的原因:铰刀外径尺寸规划值偏大或铰切削刃口有毛刺;切削速度过高;进给量不妥或加工余量过大;铰刀主偏角过大铰刀曲折;铰切削刃口上粘附着切屑瘤;刃磨时铰切削刃口摆差超差;切削液挑选不合适。
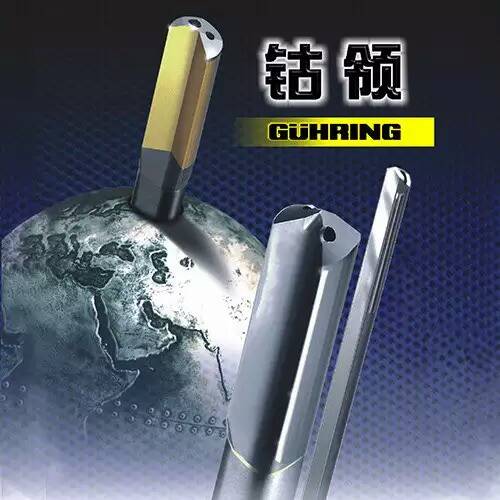
安装铰刀时锥柄表面油污未擦干净或锥面有磕碰伤;锥柄的扁尾偏位装入机床主轴后锥柄圆锥干与;主轴曲折或主轴轴承过松或损坏;铰刀浮动不灵活;与工件不同轴以及手铰孔时两手用力不均匀,使铰刀左右晃动。模具深孔钻加工时孔径增大的处理办法:根据具体情况恰当减小铰刀外径;下降切削速度恰当调整进给量或削减加工余量;恰当减小主偏角校直或报废曲折的不能用的铰刀。用油石仔细修整到合格;操控摆差在答应的范围内;挑选冷却性能较好的切削液;安装铰刀前必须将铰刀锥柄及机床主轴锥孔内部油污擦净,锥面有磕碰处用油石修光;修磨铰刀扁尾调整或更换主轴轴承;从头调整浮动卡头,并调整同轴度;留意正确操作。
上一篇: 数控深孔钻的出现满足了哪些大型行业领域?
下一篇: 深孔应该要用什么样材质的钻头呢?